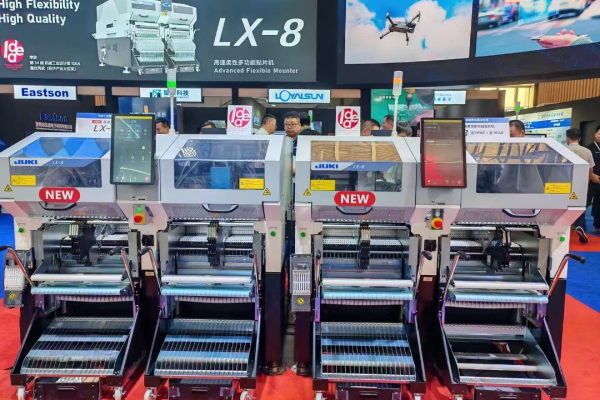
In the competitive landscape of electronics manufacturing, efficiency is paramount. As an expert in this field, I’ve seen how critical the solder paste printing process is to the overall quality and reliability of printed circuit boards. This process serves as the foundation for effective solder joints, which are essential for the performance of electronic devices. However, achieving greater efficiency in solder paste printing can be challenging. In this article, I will explore strategies and best practices to enhance efficiency in this vital manufacturing step.
To achieve more efficiency in the solder paste printing process, manufacturers must focus on optimizing equipment, enhancing operator training, refining processes, leveraging technology, and committing to continuous improvement. By addressing these areas, we can significantly boost productivity and product quality.
As we delve into this topic, it’s essential to understand the various factors that contribute to efficiency in solder paste printing. From selecting the right equipment to implementing effective training programs, each element plays a crucial role in our quest for improved performance. Let’s explore these aspects in detail.
Contents
- What Equipment Enhancements Can Improve Efficiency?
- How Does Operator Training Impact Printing Performance?
- What Role Does Process Optimization Play?
- How Can Technology Streamline Solder Paste Printing?
- What Best Practices Should Be Implemented for Continuous Improvement?
What Equipment Enhancements Can Improve Efficiency?
Investing in high-quality equipment is a critical first step toward achieving more efficiency in solder paste printing. The right solder paste printer can make a significant difference in the efficiency of the printing process. Modern printers equipped with features such as automatic alignment systems and adjustable squeegee pressure can enhance paste transfer accuracy and speed.
Upgrading to advanced solder paste printers with automation capabilities can lead to improved accuracy and consistency in paste application, ultimately boosting production efficiency.
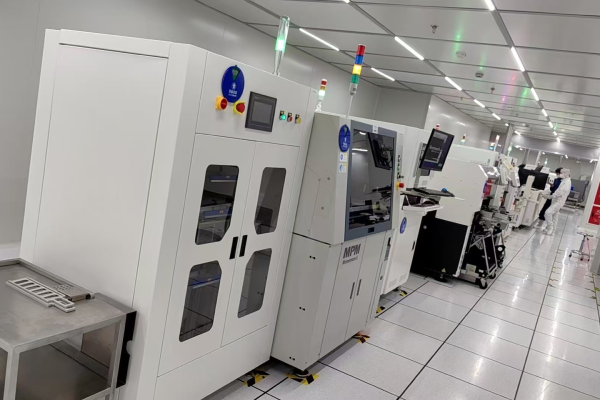
In my experience, transitioning from manual to automated printers has been one of the most impactful upgrades for many manufacturing facilities 1. Automated systems not only reduce human error but also increase speed and precision during production runs. Additionally, using laser-cut stencils with optimized aperture designs enhances paste release and minimizes defects like insufficient or excessive solder deposition. Regular maintenance of equipment is equally crucial; ensuring that printers are calibrated correctly can help prevent many common issues related to misalignment or inconsistent paste application.
How Does Operator Training Impact Printing Performance?
While equipment is vital, the skills and knowledge of operators are equally important for achieving efficiency. Properly trained operators are essential for maximizing the potential of solder paste printing equipment. They need to understand not only how to operate machines but also how to troubleshoot common issues that may arise during production.
Investing in comprehensive training programs for operators can lead to better handling of equipment and improved problem-solving skills, contributing significantly to overall efficiency.
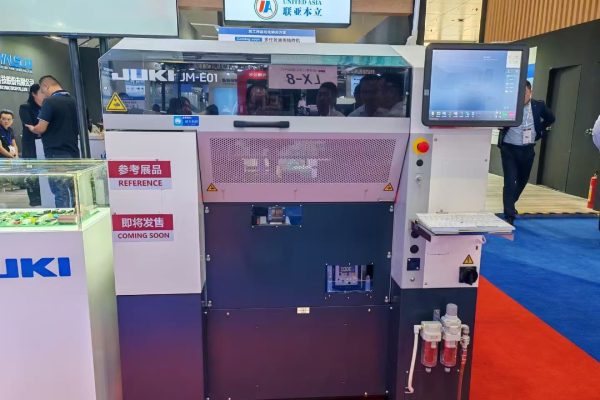
From my observations, ongoing training sessions that focus on both technical skills and best practices empower operators to identify potential issues before they escalate into significant problems. For example, teaching operators how to recognize signs of inadequate paste transfer or misalignment allows for quick adjustments that can save time and materials. Moreover, fostering a culture of teamwork and open communication among operators encourages them to share insights and solutions based on their experiences, further enhancing operational efficiency.
What Role Does Process Optimization Play?
Optimizing the solder paste printing process itself is crucial for improving efficiency. Process optimization involves analyzing each step of the solder paste printing workflow to identify areas for improvement. This includes everything from setup times to actual printing techniques.
By systematically reviewing and refining each phase of the printing process, manufacturers can eliminate bottlenecks and enhance overall productivity.
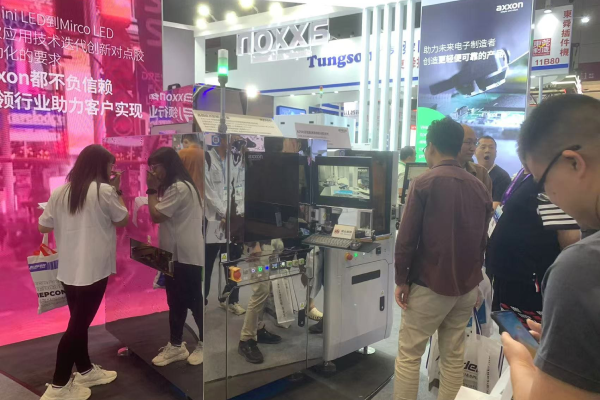
One effective approach I’ve found is implementing Lean manufacturing principles within the solder paste printing workflow. Techniques such as value stream mapping allow teams to visualize each step in the process and identify wasteful practices. For instance, reducing unnecessary movements during setup or minimizing downtime between print runs can lead to substantial gains in efficiency. Additionally, establishing standard operating procedures (SOPs) helps ensure consistency across shifts and teams, further streamlining operations.
How Can Technology Streamline Solder Paste Printing?
Advancements in technology have revolutionized many aspects of manufacturing, including solder paste printing. Integrating modern technologies such as machine learning and automation into the solder paste printing process can lead to remarkable improvements in efficiency.
Utilizing technology like automated inspection systems and data analytics tools helps manufacturers monitor performance metrics in real-time, enabling quick adjustments that enhance productivity.
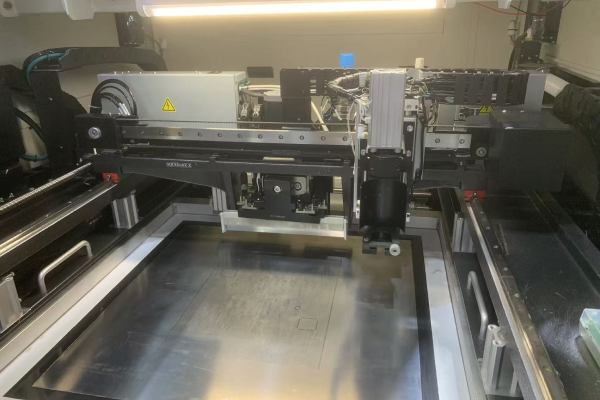
In my experience, automated optical inspection (AOI) systems provide immediate feedback on print quality during production runs. By analyzing printed PCBs for defects such as insufficient paste coverage or misalignment, these systems allow for rapid corrective actions before defects propagate downstream. Additionally, implementing data analytics tools enables manufacturers to track performance trends over time, helping identify recurring issues or inefficiencies that may require attention.
What Best Practices Should Be Implemented for Continuous Improvement?
Establishing a culture of continuous improvement is vital for sustaining efficiency gains over time. Best practices such as regular audits, feedback loops from operators, and performance reviews can help maintain high standards in solder paste printing processes.
By committing to continuous improvement initiatives and regularly reviewing processes against industry benchmarks, manufacturers can ensure sustained gains in efficiency.
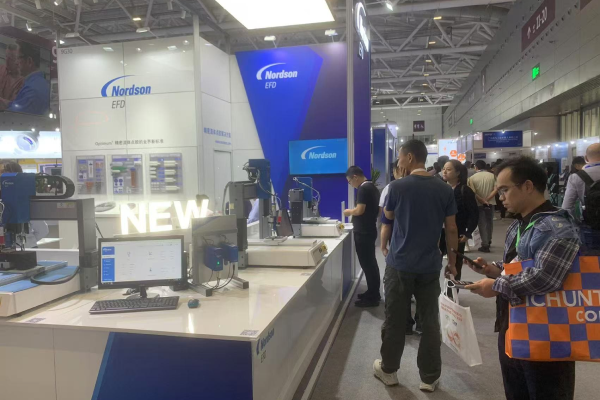
I have found that conducting regular team meetings focused on discussing performance metrics fosters a proactive approach to problem-solving. Encouraging operators to share their insights about challenges they encounter allows teams to collaboratively develop solutions that enhance overall productivity. Additionally, benchmarking against industry standards provides valuable context for evaluating performance and identifying areas where improvements are needed.
Conclusion
Achieving more efficiency in the solder paste printing process requires a holistic approach encompassing equipment upgrades, operator training, process optimization, technological integration, and a commitment to continuous improvement. By focusing on these key areas, we can significantly enhance our production capabilities while maintaining high-quality standards essential for reliable electronic devices.
As I reflect on my journey through this evolving field, I encourage you: what steps will you take today to improve your own solder paste printing processes?
- IPC – Association Connecting Electronics Industries
IPC.org
IPC is a global trade association that focuses on standardizing the assembly and production requirements of electronic equipment. Their site offers a wealth of resources, including standards, certification programs, and industry news relevant to solder paste printing and electronics manufacturing. - Wikipedia – IPC (Electronics)
IPC (electronics) – Wikipedia
This Wikipedia page provides an overview of IPC, its history, and the standards it develops for the electronics industry. It’s a good starting point for understanding the context and importance of solder paste printing standards. - CircuitNet – Solder Paste Prep Before Use
Solder Paste Prep Before Use
This article discusses best practices for preparing solder paste before use, including storage and handling tips that can influence printing efficiency and quality. - I-Connect007 – Solder Paste Printing From the Stencil’s Perspective
Solder Paste Printing From the Stencil’s Perspective
This article explores the challenges of solder paste printing from the perspective of stencil design, discussing how advancements in stencil technology can improve printing accuracy and efficiency.